
Press release news from the public relations clients of Tiziani Whitmyre, Inc.

November 30th, 2015
DECTRIS Ltd. Announces Hybrid Photon Counting (HPC) Technology Based on Newest ASIC Platform for X-ray Medical Imaging
— Visit DECTRIS Ltd. at RSNA 2015, North Hall B booth 6556 —
Chicago (USA), November 30, 2015 — DECTRIS Ltd. has announced its Hybrid Photon Counting (HPC) technology based on the newest IBEX ASIC platform for X-ray medical imaging equipment. Hybrid Photon Counting technology is enabling original equipment manufacturers (OEMs) to transform X-ray medical imaging, from computerized tomography (CT) to digital breast mammography (DBT).
DECTRIS’ pioneering HPC detection technology, powered by the new IBEX ASIC platform, outperforms current technical standards — and delivers the best possible image quality based on single X-ray detection, highest sensitivity and lowest dose. Hybrid Photon Counting technology provides:
- Lowest possible dose — achieving the best signal-to-noise ratio via a noise-free detection with a high dynamic range and no dark current
- Radiation-hardness for ultimate long-term stability — via a specific design
- Very high frame rates — via dedicated ASIC and electronics
- Native spectral information for color X-ray imaging — via energy discrimination
- Almost perfect spatial resolution — via direct detection
Previously, X-ray detection in medical imaging has mainly relied on the indirect methods utilized by traditional integrating detectors lacking energy discrimination. Not only does the new IBEX ASIC sense every single photon in an X-ray, but it also provides the flexibility of two readout modes: A high resolution mode to detect subtle details and a spectral one to add color information to grey-scale radiology.
For OEMs, pairing Hybrid Photon Counting with advanced new X-ray medical imaging instruments and analysis algorithms, the additional spectral information will open up a new dimension in specificity.
DECTRIS is the world’s acknowledged leader in HPC detection, having produced more than 8,000 HPC detector modules to date — far more than any other source — for a variety of applications in science and industry.
As the leader, DECTRIS empowers medical imaging OEMs to shift the radiology into the era of native spectral X-ray imaging. The HPC proposition of geometrical accuracy, image quality, sensitivity at highest spectral fidelity will pave the way to precision medicine in a cost effective and safe way. Improved diagnostics (detection, characterization) based on existing contrast agents and new targeted biomarkers, will ultimately enable the logging of therapy responses.
For more information, visit DECTRIS Ltd. at RSNA 2015 in North Hall booth 6556. Or visit the DECTRIS website at http://medical.dectris.com or call +41.56.500.2180
About DECTRIS
As the technology leader in X-ray detection, DECTRIS aims to continuously improve measurement quality to enable new findings and innovative results in science, industry, and medicine. DECTRIS X-ray detectors make optimum use of the company’s pioneering Hybrid Photon Counting (HPC) technology. It has transformed basic research at synchrotron light sources, as well as in laboratory and industrial X-ray applications worldwide. For more information, visit http://medical.dectris.com or call +41.56.500.2180.
Tags: computerized tomography, digital breast mammography, HPC detection, hybrid photon counting, IBEX ASIC, X-ray medical imaging

November 18th, 2015
Using New Portable ED-XRF Instruments At-Line Can Provide Reliable Coat-Weight Measurement – New Application Brief from SPECTRO
Kleve, Germany — November 18, 2015 — A new application brief explains how a new generation of portable energy dispersive X-ray fluorescence (ED-XRF) instruments can provide performance comparable to laboratory-based systems and offer the flexibility to be easily moved to various process points to provide high-accuracy Quality Assurance (QA)/Quality Control (QC) for producers of steel or aluminum sheets. The brief, “At-Line Analysis of Coat Weight on Steel and Aluminum Sheets using ED-XRF Spectroscopy at the Process Line,” is available to download at http://goo.gl/CwVs4S from SPECTRO Analytical Instruments, a leading manufacturer of advanced instruments.
Steel and aluminum sheet producers often coat their products to protect them from rust or corrosion or to achieve a variety of objectives. The sheets go through a number of chemical processes to convert the steel or aluminum into the coating material. The consistency of coating thickness — commonly referred to as “coat weight” — is vital to successful production quality and requires advanced analytical techniques. Depending on substrate and customer requirements, analytical instruments might be needed to detect and measure the thickness of a wide variety of coating materials.
X-ray fluorescence (XRF) spectroscopy is an excellent technology for coat-weight analysis and can be performed with a variety of instruments, ranging from handheld systems to laboratory-based wavelength-dispersive X-ray spectroscopy (WD-XRF) instruments. Laboratory instruments are expensive and can delay process schedules, as samples must be taken from the line to the lab. Handheld XRF systems are popular but have many practical and analytical drawbacks.
Now, new portable ED-XRF instruments such as the SPECTROSCOUT portable analyzer have excellent analytical range and precision exhibiting very low limits of detection. Using this instrument at-line has been shown to provide reliable coat-weight measurement for a wide range of coating materials, including iron, zinc, manganese phosphate, zirconium, chromium and titanium. The new application brief, “At-Line Analysis of Coat Weight on Steel and Aluminum Sheets using ED-XRF Spectroscopy at the Process Line,” provides the details. Download the brief at http://goo.gl/CwVs4S.
About SPECTRO:
SPECTRO, a unit of the Materials Analysis Division of AMETEK, Inc., manufactures advanced instruments, develops the best solutions for elemental analysis for a broad range of applications, and provides exemplary customer service.
SPECTRO’s products are known for their superior technical capabilities that deliver measurable benefits to the customer. From its foundation in 1979 until today, more than 40,000 analytical instruments have been delivered to customers around the world.
AMETEK, Inc. is a leading global manufacturer of electronic instruments and electromechanical products with more than 15,000 colleagues at nearly 150 operating locations and sales and service operations in the United States and 30 other countries around the world.
For more information, visit www.spectro.com.
Tags: coat weight, coat weight on aluminum, coat weight on steel, coat-weight analysis, ED-ERF, energy dispersive X-ray fluorescence, metal analysis, metal surface coatings

November 16th, 2015
Honeywell Announces Hearing Conservation Toolbox Mobile Application
One-Stop Information Resource for Workplace Hearing Safety for Use on Apple iPad®
SMITHFIELD, R.I., Nov 16, 2015 — Noise-induced hearing loss (NIHL) is a major concern of safety managers, affecting approximately 22 million U.S. workers and costing $242 million annually in workers’ compensation, according to the Centers for Disease Control (CDC).
Developed in close cooperation with audiologists and safety professionals, Honeywell’s new Howard Leight Hearing Conservation Toolbox mobile application for iPad® is an easily accessible point-of-use resource of interactive tools and educational materials for safety managers to use in support of workplace hearing safety programs.
Subtitled “Hearing Conservation Starts Here,” the app features the latest information on the risks of occupational noise, hearing conservation program best practices, and practical instruction on the testing, selection, fitting, and use of hearing protection. The app offers instant access to:
- Hearing conservation program information and checklists on NIHL, ear anatomy, regulations, choosing and fitting hearing protectors and more;
- Informative articles written by Honeywell audiologists based on their experience hosting hundreds of “Howard Leight® HearForever™: Best Practices in Effective Hearing Conservation” seminars about preventing job-related hearing loss;
- Educational videos on the auditory system, the personal effects of NIHL, the importance of fit testing, and more;
- A “Noise Thermometer” infographic that quickly communicates the impact of exposure to both on- and off-the-job sources of noise by mapping the sound levels to a thermometer illustration;
- An interactive “Noise Wheel” explaining the factors, such as fit, protection, size, and comfort, to consider when choosing hearing protection products;
- Hearing protector fit instructions, illustrations, tips, and videos demonstrating the proper wear and use of earplugs and earmuffs;
- Maintenance and care information for earplugs and earmuffs to ensure the effectiveness of hearing protectors;
- Details of Honeywell’s VeriPRO earplug fit-testing system which enables safety managers to easily create an accurate, real-world picture of their employees’ hearing protection;
- Complete catalog of hearing protection products with attenuation ratings and a dealer locator with where-to-buy information.
Download the new Honeywell Hearing Conservation Toolbox mobile app for iPad® from iTunes at http://hwll.co/HearingApp.
# # #
About Honeywell
Honeywell (www.honeywell.com) is a Fortune 100 diversified technology and manufacturing leader, serving customers worldwide with aerospace products and services; control technologies for buildings, homes, and industry; turbochargers; and performance materials. For more news and information on Honeywell, please visit www.honeywellnow.com.
About Honeywell Industrial Safety
Honeywell Industrial Safety (HIS), part of Honeywell Automation and Control Solutions, provides comprehensive solutions to help organizations manage workplace safety in an increasingly complex world. HIS helps organizations with connected, real-time safety intelligence to respond to safety threats, manage risk to the business and improve productivity. In addition to offering the broadest range of industrial safety products — from personal protection gear for a worker’s eyes, ears and head, to fall protection harnesses and respiratory protection, software, first responder gear and toxic gas monitors — HIS helps organizations make better decisions by connecting sensors throughout customers’ operations to deliver an accurate picture of safety at all times.
Tags: Apple, ear muffs, ear plugs, earmuffs, earplugs, hearing conservation, hearing loss, Hearing Protection, iPad, iPad add, NIHL, noise-induced hearing loss, personal protection equipment, PPE, worker safety

November 13th, 2015
New White Paper from SPECTRO: Why Overcoming Matrix Effects With XRF Analysis Is Critical For High-Accuracy Results
Kleve, Germany — November 4, 2015 — A new white paper explains why overcoming matrix effects associated with X-ray fluorescence (XRF) analysis is critical to achieving consistent high-accuracy results. The paper, titled “Mitigating Matrix Effects with Advanced When Using XRF for High-Accuracy Elemental Analysis,” is available to download at http://goo.gl/5tIKb9 from SPECTRO Analytical Instruments, a leading manufacturer of advanced instruments.
A great advantage of energy dispersive x-ray fluorescence (ED-XRF) analysis for rapid screening analysis is its ability to measure samples directly with a minimum of preparation. Realizing this benefit, however, requires eliminating potential errors that can result when atoms in the sample matrix influence the fluorescence of others and thus the intensities measured by the spectrometer are influenced. Such effects, which include absorption and enhancement, when taken collectively, are referred to generally as matrix effects. For quality control applications, when the sample matrix is known or can be matched, a variety of standards-based XRF calculation procedures are available to compensate for undesirable matrix effects.
However, creating the right basis for consistently high-accuracy results requires additional spectra handling functionality to determine the correct net intensities of the measured spectra. The new white paper, “Mitigating Matrix Effects with Advanced Spectra-Handling Functionality When Using XRF for High-Accuracy Elemental Analysis,” explains why this additional functionality is a critical aspect of overcoming matrix effects and ensuring those consistently high-accuracy results. Download the new white paper from http://goo.gl/5tIKb9.
About SPECTRO:
SPECTRO, a unit of the Materials Analysis Division of AMETEK, Inc., manufactures advanced instruments, develops the best solutions for elemental analysis for a broad range of applications, and provides exemplary customer service.
SPECTRO’s products are known for their superior technical capabilities that deliver measurable benefits to the customer. From its foundation in 1979 until today, more than 40,000 analytical instruments have been delivered to customers around the world.
AMETEK, Inc. is a leading global manufacturer of electronic instruments and electromechanical products with more than 15,000 colleagues at nearly 150 operating locations and sales and service operations in the United States and 30 other countries around the world.
Tags: ED-XRF analysis, matrix effects, Spectra-Handling, X-ray fluorescence, XRF

October 29th, 2015
SPECTRO Opens New State-of-the-Art Application and Demonstration Laboratory in Irvine, California
IRVINE, Calif., Oct. 28, 2015 – SPECTRO Analytical Instruments, Inc., a leading manufacturer of advanced instruments, has opened a new state-of-the-art application and demonstration laboratory in Irvine, California.
SPECTRO developed the laboratory “due to the remarkable growth in demand for application development support and strong interest in our next generation instrument lines,” said Mark Grey, Vice President & General Manager, SPECTRO Analytical Instruments.
The laboratory features the latest in SPECTRO instrumentation and technology for elemental analysis — including inductively coupled plasma optical emission spectrometry (ICP-OES), X-ray fluorescence (XRF) spectroscopy, inductively coupled plasma mass spectrometry (ICP-MS), and optical emission spectroscopy using arc and spark excitation (Arc Spark OES).
Grey encouraged laboratory managers, scientists, technicians, and other professionals to utilize the laboratory’s state-of-the-art SPECTRO analyzers and staff of lab technicians to assist in their application research, development, and trouble-shooting projects.
The laboratory will also serve to host technical events, training sessions, and instrument and application demonstrations, Grey said.
The SPECTRO Application/Demonstration Laboratory is located at 2031 Main Street, Irvine, Calif.
About SPECTRO:
SPECTRO, a unit of the Materials Analysis Division of AMETEK, Inc., manufactures advanced instruments, develops the best solutions for elemental analysis for a broad range of applications, and provides exemplary customer service.
SPECTRO’s products are known for their superior technical capabilities that deliver measurable benefits to the customer. From its foundation in 1979 until today, more than 40,000 analytical instruments have been delivered to customers around the world. For more information, visit www.spectro.com.
AMETEK, Inc. is a leading global manufacturer of electronic instruments and electromechanical products with more than 15,000 colleagues at nearly 150 operating locations and sales and service operations in the United States and 30 other countries around the world.
Tags: analytical instruments, ICP-OES, SPECCTRO, spectrometers, spectroscopy, XRF

October 29th, 2015
First Commons Bank Reaches $293 Million in Total Assets in Q3 – Representing 15% Growth Year-to-Date; Net Deposits and Net Loans Increased 17%
NEWTON, Mass., Oct. 29, 2015 – First Commons Bank of Newton, Mass., today reported that it achieved a new high point of $293 million in Total Assets as of September 30, 2015, representing a 15% increase versus December 31, 2014, and a 4% increase versus last quarter ended June 30, 2015. Total Deposits grew to $250 million or 17% year-to-date, and 4% versus last quarter, with the core deposit areas of checking, money market and CD’s under $250,000 experiencing most of the growth. Net Loans increased to $249 million as of September 30, 2015, representing a 17% increase year-to-date, and 7% versus last quarter.
Tony Nuzzo, Chairman, President and CEO of First Commons Bank said, “We are very pleased with our growth in assets, deposits, and loans this quarter. For example, Net Loans increased $15 million or 7% in this past quarter alone. Additionally, with Total Assets of $293 million, First Commons Bank is in the top 35% of the more than 6,200 banks in the US filing FDIC Call Reports on June 30, 2015.”
Net income for the 3-month period ended September 30, 2015, was $200 thousand compared to $254 thousand for last quarter. Mr. Nuzzo said, “Our exceptional Net Loan growth this quarter resulted in a much higher than expected increase to the Allowance for Loan Losses which impacted this quarter’s income. Yet, we remain very pleased with our outstanding credit quality as non-performing loans were zero at quarter end.”
Tangible Book Value on September 30, 2015, was $10.00 per share, with approximately $31 million in equity and a Tier 1 Capital Ratio to Average Assets for the quarter of 10.75%.
First Commons Bank’s financial results are available on the FDIC’s Web site at: https://goo.gl/ZqXzjk.
About First Commons Bank
First Commons Bank, N.A., is a nationally chartered, FDIC-insured full-service community bank, dedicated to serving the businesses and individuals of Newton, Wellesley, Waltham, and eastern Massachusetts. The bank opened for business on July 22, 2009. Locations include its headquarters at 718 Beacon Street in Newton Centre, Mass., and 161 Linden Square in Wellesley, Mass. Visit the First Commons Bank website at http://www.firstcommonsbank.com. Follow the bank on Facebook at http://facebook.com/firstcommonsbank and on Twitter at http://twitter.com/firstcommonsbnk.
First Commons Bank, N.A. | |||||||
Balance Sheet | |||||||
(Unaudited) | |||||||
September 30, | December 31, | ||||||
2015 | 2014 | ||||||
(dollars in thousands) | |||||||
Assets | |||||||
Cash and Due from Banks | $ | 1,807 | $ | 1,516 | |||
Interest-bearing demand deposits with other banks | 140 | 123 | |||||
Money Market Mutual Funds | 182 | 162 | |||||
Federal funds sold | 25,500 | 30,900 | |||||
Cash and Cash equivalents | 27,629 | 32,701 | |||||
Interest-bearing time deposits with other banks | 7,579 | 2,205 | |||||
Investment in held -to-maturity securities | 2,000 | 0 | |||||
Federal Home Loan Bank Stock, at cost | 956 | 956 | |||||
Federal Reserve Bank Stock, at cost | 1,719 | 1,395 | |||||
Loans, net | 249,291 | 212,686 | |||||
Premised and equipment | 1,014 | 1,156 | |||||
Accrued interest receivable | 832 | 642 | |||||
Deferred income tax asset, net | 1,225 | 1,859 | |||||
Other assets | 842 | 332 | |||||
Total Assets | $ | 293,087 | $ | 253,932 | |||
Liabilities and Stockholders’ Equity | |||||||
Deposits: | |||||||
Noninterest-bearing | $ | 26,150 | $ | 18,998 | |||
Interest-bearing | 224,519 | 194,425 | |||||
Total Deposits | 250,669 | 213,423 | |||||
Federal Home Loan Bank Advances | 10,000 | 10,000 | |||||
Other Liabilities | 1,228 | 1,867 | |||||
Total Liabilities | 261,897 | 225,290 | |||||
Stockholders’ equity | |||||||
Common Stock, par value .01; authorized 10,000,000 shares, 3,120,122 and 2,950,532 shares issued and outstanding as of September 30, 2015 and December 31, 2014 respectively | 31 | 30 | |||||
Paid-in Capital | 33,393 | 31,508 | |||||
Accumulated deficit | -2,234 | -2,896 | |||||
Total stockholders’ equity | 31,190 | 28,642 | |||||
Total liabilities and stockholders’ equity | $ | 293,087 | $ | 253,932 |
First Commons Bank, N.A. | |||||||
Statement of Income | |||||||
(Unaudited) | |||||||
Nine Months Ended | |||||||
September 30 | |||||||
2015 | 2014 | ||||||
(Dollars in thousands) | |||||||
Interest Income: | |||||||
Interest and fees on loans | $ | 8,187 | $ | 8,092 | |||
Interest on securities | 67 | 21 | |||||
Other interest | 69 | 30 | |||||
Total interest income | 8,323 | 8,143 | |||||
Interest Expense | |||||||
Interest on deposits and borrowings | 1,818 | 1,691 | |||||
Total Interest Expense | 1,818 | 1,691 | |||||
Net interest income | 6,505 | 6,452 | |||||
Provision for loan losses | 303 | 0 | |||||
Net interest income after provision for loan losses | 6,202 | 6,452 | |||||
Noninterest income | |||||||
Service charges on deposit accounts | 50 | 41 | |||||
Gain on sale of available-for-sale securities | 0 | 0 | |||||
Gain on sale of loans | 134 | 24 | |||||
Other income | 115 | 76 | |||||
Total noninterest income | 299 | 141 | |||||
Noninterest expense: | |||||||
Salaries and employee benefits | 3,080 | 2,701 | |||||
Occupancy expense | 646 | 630 | |||||
Equipment expense | 155 | 185 | |||||
Professional fees | 323 | 328 | |||||
Regulatory assessment | 164 | 229 | |||||
Other expense | 990 | 863 | |||||
Total noninterest expense | 5,358 | 4,936 | |||||
Income (loss) before income tax expense (benefit) | 1,143 | 1,657 | |||||
Income Tax expense (benefit) | 482 | 684 | |||||
Net Income (Loss) | $ | 661 | $ | 973 |
Tags: banking, community banks, first commons bank, Newton, Wellesley

October 21st, 2015
SPECTRO and CEM Host Seminars Exploring Latest Technical Advances in ICP-OES and XRF Spectroscopy
IRVINE, CA, October 21, 2015 — A series of technical seminars exploring the latest advances in inductively coupled plasma optical emission spectrometry (ICP-OES) and X-ray fluorescence (XRF) spectroscopy hosted by SPECTRO Analytical Instruments, Inc. and CEM Corporation, two leaders in atomic spectroscopy and microwave digestion, are scheduled for October and November in seven western U.S. cities.
As the field of spectroscopy continually advances, the seminars afford lab managers, scientists, technicians, and other professionals the opportunity to get an up-to-date overview of the latest advances in spectroscopy technology and supporting processes from experts dedicated to the field. The seminars’ interactive format will enable attendees to discuss their applications and issues, learn practical tips, and see how peers are leveraging these technologies to improve their own analyses.
Titled “The SPECTRO/CEM Seminar Tour: The latest technical advances in ICP-OES and XRF spectroscopy,” the morning-long seminar will include such topics as: “Latest Advances in ICP Technology for Diverse Applications,” “Energy Dispersive XRF Systems as Versatile Tool for Industry, Academia and Regulatory Applications,” and “Using Microwave Digestion to Optimize Your Laboratory’s Work Flow.” Small group discussions will highlight applications in ICP, Microwave Digestion, and XRF; an overview of SPECTRO and CEM instrumentation will be featured; and a continental breakfast provided.
The seminars will take place from 8 a.m. to noon at:
- Phoenix, AZ (Tuesday, Oct. 27) Holiday Inn & Suites Phoenix Airport, 3220 S. 48th Street , Phoenix, AZ 85040
- Buena Park, CA (Thursday, Oct. 29) Courtyard Anaheim Buena Park, 7621 Beach Boulevard Buena Park, CA 90620
- Union City, CA (Tuesday, Nov. 3) Crowne Plaza Silicon Valley, 32083 Alvarado Niles Rd, Union City, CA 94587
- W- Reno, NV (Wednesday, Nov. 4) Hyatt Place Reno Tahoe Airport, 1790 East Plumb Lane, Reno, Nevada, USA, 89502
- Portland, OR (Friday, Nov. 6) Courtyard Portland Downtown Convention Center, 435 NE Wasco Street, Portland, Oregon 97232
- Richland, WA (Tuesday, Nov. 10) Courtyard by Marriott, Richland Columbia Point, 480 Columbia Point Drive, Richland, WA 99352
- Westminster, CO (Thursday, Nov. 12) Double Tree Hotel, 8773 Yates Dr, Westminster, CO 80031
Registration is limited to the first 35 registrants for each location. The agenda is designed to best benefit laboratory managers, directors and supervisors; scientists, principal investigators and project leaders; post-doctoral fellows, professors and instructors; and technicians and research assistants.
For more information or to register, visit http://goo.gl/t8hSXY.
About SPECTRO:
SPECTRO, a unit of the Materials Analysis Division of AMETEK, Inc., manufactures advanced instruments, develops the best solutions for elemental analysis for a broad range of applications, and provides exemplary customer service.
SPECTRO’s products are known for their superior technical capabilities that deliver measurable benefits to the customer. From its foundation in 1979 until today, more than 40,000 analytical instruments have been delivered to customers around the world.
AMETEK, Inc. is a leading global manufacturer of electronic instruments and electromechanical products with more than 15,000 colleagues at nearly 150 operating locations and sales and service operations in the United States and 30 other countries around the world.
Tags: ED-XRF, energy dispersive X-ray fluorescence spectrometers, ICP, ICP spectrometers, ICP-OES, spectroscopy, X-ray fluorescence, XRF

October 20th, 2015
New Application Brief: Analysis of Oils Using ICP-OES With Radial Plasma Observation
A new application brief explains how the use of inductively coupled plasma optical emission spectrometry (ICP-OES) with radial plasma observation provides a simple, fast, accurate and precise method for the analysis of trace elements, wear metals, additives, chlorine, and sulfur in oil matrices. Titled, “Analysis of Oils Using ICP-OES with Radial Plasma Observation,” the brief is available to download at http://goo.gl/eEqVNn from SPECTRO Analytical Instruments, a leading manufacturer of advanced instruments.
The elemental analysis of oils is important for many petroleum laboratories and refining processes. Samples can be crude oils, new and used lubricating oils, gas or fuel oils, and the elements to be analyzed vary with the product.
In crude oils, sulfur, alkali elements, vanadium, copper, nickel, iron, arsenic and phosphorus are of importance to characterize the oil and to avoid deactivation of catalysts in the refining process. For wear metals in lubricating oils, aluminum, copper, nickel or iron can be indicative of wear in oil-wetted components. Other elements like silicon, magnesium or potassium can be indicative of contamination of the oil. Also, the correct addition of elements, such as molybdenum, calcium, barium, phosphorus, and zinc should be monitored.
ICP-OES instruments, due to their multi element capability, high dynamic linear range, stability, and low detection limits, are suggested in several standard procedures for oil and fuel analysis.
The paper details how ICP-OES, using the new SPECTRO ARCOS ICP-OES instrument with radial plasma observation, can provide a fast, simultaneous determination of trace elements, wear metals, additives, chlorine, and sulfur in oil. The easy sample preparation and low detection limits, combined with the high sample throughput of the method ensures low costs of analysis and enables its use for various applications in the petrochemical field.
To download the application brief, “Analysis of Oils Using ICP-OES with Radial Plasma Observation,” visit http://goo.gl/eEqVNn.
About SPECTRO:
SPECTRO, a unit of the Materials Analysis Division of AMETEK, Inc., manufactures advanced instruments, develops the best solutions for elemental analysis for a broad range of applications, and provides exemplary customer service.
SPECTRO’s products are known for their superior technical capabilities that deliver measurable benefits to the customer. From its foundation in 1979 until today, more than 40,000 analytical instruments have been delivered to customers around the world.
AMETEK, Inc. is a leading global manufacturer of electronic instruments and electromechanical products with more than 15,000 colleagues at nearly 150 operating locations and sales and service operations in the United States and 30 other countries around the world.
Tags: elemental analysis, fuel analysis, ICP-OES, oil analysis, Oils, Radial Plasma, spectrometers, spectroscopy

October 12th, 2015
Miller Fall Protection Catalog Offers Advanced Safety Solutions for Working at Height
The new Miller Fall Protection catalog offers in-depth product descriptions and additional support for those who need to perform their jobs efficiently and safely while working at height. Miller offers technologically advanced, yet easy-to-work-with products designed to meet a variety of applications or environments.
The new catalog, organized for easy browsing according to the ABC’s of Fall Protection, features Miller® Anchorage Connectors & System Kits, Body Wear, Connecting Devices, Descent/Rescue & Confined Space, Engineered Solutions, and Fall Prevention & Protection Training. Additional catalog resources offer help with understanding, inspecting and maintaining personal fall arrest systems; calculating fall clearances; donning harnesses; and more.
Access the Miller Fall Protection catalog via the Honeywell Safety Products Media App for both iPhone(R) and iPad(R), available from https://itunes.apple.com/us/app/safety-media/id949600294?ls=1&mt=8.
Tags: fall prevention, fall protection, personal protective equipment, PPE, work at height, worker safety

October 8th, 2015
ASCO Numatics Introduces Repairable Round Line Cylinders Featuring Comprehensive Mounting and Threading Options

ASCO Numatics Introduces Repairable Round Line Cylinders Featuring Comprehensive Mounting and Threading Options
Novi, Michigan, U.S.A. — October 8, 2015 — ASCO Numatics has introduced the Numatics 488 Series Repairable Round Line Cylinders that come with magnets and bumpers as standard features. The 488 Series also is available with optional adjustable cushions, plus has more mounting and thread-type options than competitive products in its class.
“Numatics’ new repairable cylinders offer more mounting styles, port thread types, and rod end configurations than any other product on the market,” said Robert W. Kemple, Jr., executive vice president, sales and marketing — Americas, ASCO Numatics. “This wide range of options will provide design engineers and maintenance technicians with the flexibility to create a perfect fit out of the box for their application.”
Numatics 488 Series Repairable Round Line Cylinders are available in metric sizes, making them highly desirable for original equipment manufacturers (OEMs). With construction that is more robust than nonrepairable cylinders, the 488 Series is more durable and reliable to accommodate the high cycle rates found in packaging and automotive applications.
The 488 Series pneumatic cylinders are designed with a flush round profile tube and encapsulated cushions for a cleaner, more hygienic and aesthetic look. Their smooth surfaces are resistant to corrosion buildup and create more attractive OEM equipment.
Other 488 Series features include:
- Quick shipment through the Numatics 5Day Express program
- Seventeen available mounting styles including rear spherical eye adjustable mounts and detachable nose mounts
- Proven 25% faster than competitive standards with all full-flow port thread types (BSPT, NPTF, G, and M7)
- Standard rod end options including female and male rod threads
- Wide maximum operating pressure and temperature ranges
- Available positioning sensors
- Industry-leading, proven heavy-duty piston wear band that is more than 50% wider than competitive offerings
“Numatics’ 488 Series Repairable Round Line Cylinders are more compact, making them easier to install and repair,” said Kemple. “Their mounting and threading flexibility means OEMs can rapidly change machine designs. And their interchangeability with competitive products makes them well suited for MRO replacement,” he said.
The 488 Series cylinders are ideal for packaging equipment such as sorting conveyors, pusher stations, case packing, bottle-forming machines, and palletizing equipment. General automation and automotive applications include material handling equipment, component conveyors, clamping for frame weld processing, and suspension systems.
For more information, contact Numatics at 1-888-NUMATICS (1-888-686-2842), e-mail insidesales@numatics.com, or visit www.numatics.com/488.
About ASCO Numatics
ASCO Numatics, an Emerson company, offers comprehensive fluid automation solutions, including fluid control and fluid power products, for a wide range of industry-focused applications. The ASCO Numatics product line in North America consists of more than 50,000 valves, an extensive selection of air preparation equipment, and a full line of actuation products. ASCO products include solenoid pilot valves, angle body piston valves, linear indicators, redundant control systems, and pressure sensors. The Numatics line covers valve manifolds, cylinders, grippers, filters, regulators, and lubricators. For more information about ASCO Numatics products, visit www.asconumatics.com.
About Emerson
Emerson (NYSE: EMR), based in St. Louis, Missouri (USA), is a global leader in bringing technology and engineering together to provide innovative solutions for customers in industrial, commercial, and consumer markets around the world. The company is comprised of five business segments: Process Management, Industrial Automation, Network Power, Climate Technologies, and Commercial & Residential Solutions. Sales in fiscal 2014 were $24.5 billion. For more information, visit Emerson.com.
Tags: ASCO, Numatics, pneumatic cylinders, Repairable Round Line Cylinders, Round Line Cylinders

B2B News is proudly powered by WordPress.
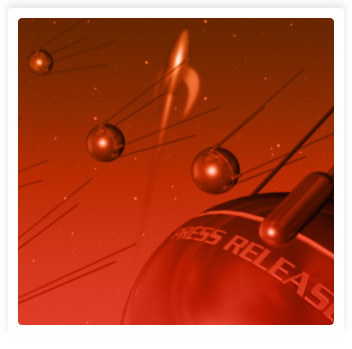
About Tiziani Whitmyre
Tiziani Whitmyre Inc.'s public relations expertise is in technology & life sciences PR. We work with companies from small business startups to global leaders. Unlike traditional firms, we are very flexible in our PR services and combine the expertise of large agency professional talent within the flexibility of a boutique. We help clients generate sales leads, launch new products, enter new markets, establish technical leadership, and achieve other business goals. We craft and execute cost-effective, results-focused efforts that integrate traditional and Web 2.0 solutions as discrete projects, targeted campaigns, on-going PR programs, or elements in an integrated marketing program. Our industry experience is deep and includes analytical instruments, biotechnology, ecommerce, food and dairy, healthcare, high technology, laboratory sciences, life sciences, machinery, manufacturing, medical products, pharmaceuticals, professional services, and software
